在高端装备制造领域,如何快速获取具备优异机械性能的极品装备始终是行业痛点。传统锻造工艺受制于材料利用率低、成型精度差、性能调控困难等瓶颈,难以满足航空航天、精密仪器等领域对装备性能的严苛要求。近年来,基于熔炼系统革新的锻造工艺创新,通过材料提纯、成型优化、智能控制三大技术突破,正在重构高端装备的制造范式。
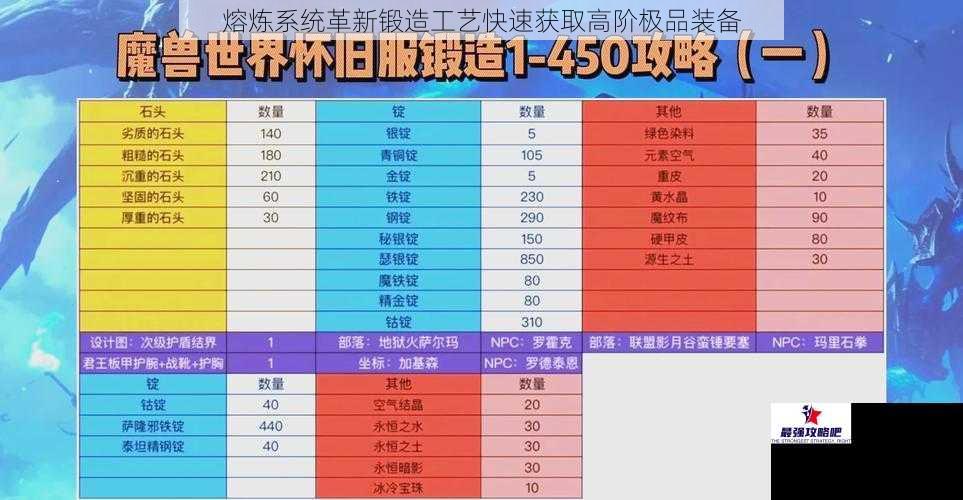
熔炼系统革新赋能材料基因优化
现代感应熔炼技术采用电磁悬浮熔炼(Electromagnetic Levitation Melting)结合真空脱气工艺,将金属材料含氧量控制在10ppm以下。某航空发动机叶片制造案例显示,通过双频电磁搅拌技术(50Hz+150Hz复合磁场)可使铝合金熔体温度均匀性提升70%,晶粒细化至12μm以下。这种微观组织的精准调控,为后续锻造工艺提供了理想的材料基础。
真空自耗电弧重熔(VAR)技术通过精确控制熔池形态,有效消除铸锭宏观偏析。美国某军工企业采用多级真空系统(10^-3Pa级)配合动态熔速控制,使钛合金铸锭成分波动范围缩小至±0.15%,显著提升材料批次稳定性。这种材料均质化突破,使锻造工序的工艺窗口拓宽了40%以上。
锻造工艺创新的三维突破
等温锻造技术(Isothermal Forging)通过模具温度与工件保持动态平衡,将铝合金变形抗力降低至常规锻造的1/3。某航天结构件生产数据显示,在480℃等温条件下,7075铝合金的极限变形量从常规工艺的60%提升至95%,材料利用率提高52%。配合超塑性成形技术,可制造出壁厚0.8mm、公差±0.05mm的复杂薄壁构件。
增量成形工艺(Incremental Forming)采用多轴联动数控系统,通过局部连续变形实现整体成型。德国某机床企业开发的5轴增量锻造中心,将大型锻件的加工工序从12道缩减至3道,成型精度达到IT8级。这种离散-连续复合成形模式,使模具成本降低65%,特别适合小批量多品种生产。
智能锻造系统集成数字孪生技术,构建工艺参数与性能指标的动态映射模型。某轴承企业建立的锻造知识图谱包含2800组工艺数据集,通过机器学习算法实现变形温度、应变速率、冷却速度的协同优化,使轴承钢的疲劳寿命提升2.3倍。实时质量监测系统采用高频声发射(100kHz采样)技术,可在线识别0.1mm级内部缺陷。
熔锻协同制造的工业化实践
某燃气轮机叶片制造商采用"真空熔炼+等温锻造+定向凝固"的集成工艺,使单晶高温合金叶片的持久强度达到850MPa@900℃。通过熔炼阶段的成分梯度设计和锻造阶段的应变场控制,成功实现叶片榫头-叶身区域的性能差异化制造,使涡轮前温度耐受能力提升150℃。
在医疗器械领域,钴铬合金关节假体的熔锻协同制造具有示范意义。电子束熔炼(EBM)技术将杂质元素总量控制在0.01%以下,配合微锻造(Micro-forging)工艺在β相区进行多向压缩,使假体耐磨性提高3倍的同时保持弹性模量匹配人体骨骼(18-25GPa)。该技术使翻修手术间隔周期从10年延长至25年。
技术演进趋势与挑战
随着高熵合金、金属基复合材料等新型材料的应用,熔锻协同制造面临新的技术挑战。激光熔覆锻造(Laser Cladding Forging)技术通过逐层熔覆与热机械处理的交替进行,正在突破传统工艺的材料限制。某研究机构开发的梯度功能材料制备系统,可实现材料硬度从基体到表面200HV到800HV的连续过渡。
工艺链数字化整合成为重要发展方向。基于区块链技术的质量追溯系统,可将熔炼参数、锻造工艺、检测数据全程上链,构建不可篡改的质量档案。某汽车零部件供应商应用该技术后,产品召回率下降92%,质量认证周期缩短40%。
当前技术瓶颈集中在跨尺度模拟领域。从熔炼过程的分子动力学模拟(纳米级)到锻造过程的有限元分析(毫米级),尚未建立完整的数字孪生体系。欧盟某联合研究项目开发的跨尺度建模平台,通过机器学习算法桥接不同维度的物理模型,使工艺优化效率提升8倍。
熔锻协同制造系统的革新,本质上是对材料基因、能量场调控、信息感知三大要素的系统性重构。这种变革不仅带来装备性能的飞跃,更重塑了高端制造的产业生态。随着5G+MEC边缘计算、量子传感等新技术的渗透,未来的极品装备制造将向着"材料-工艺-性能"的精准定向制造持续演进,开启高端装备智造的新纪元。